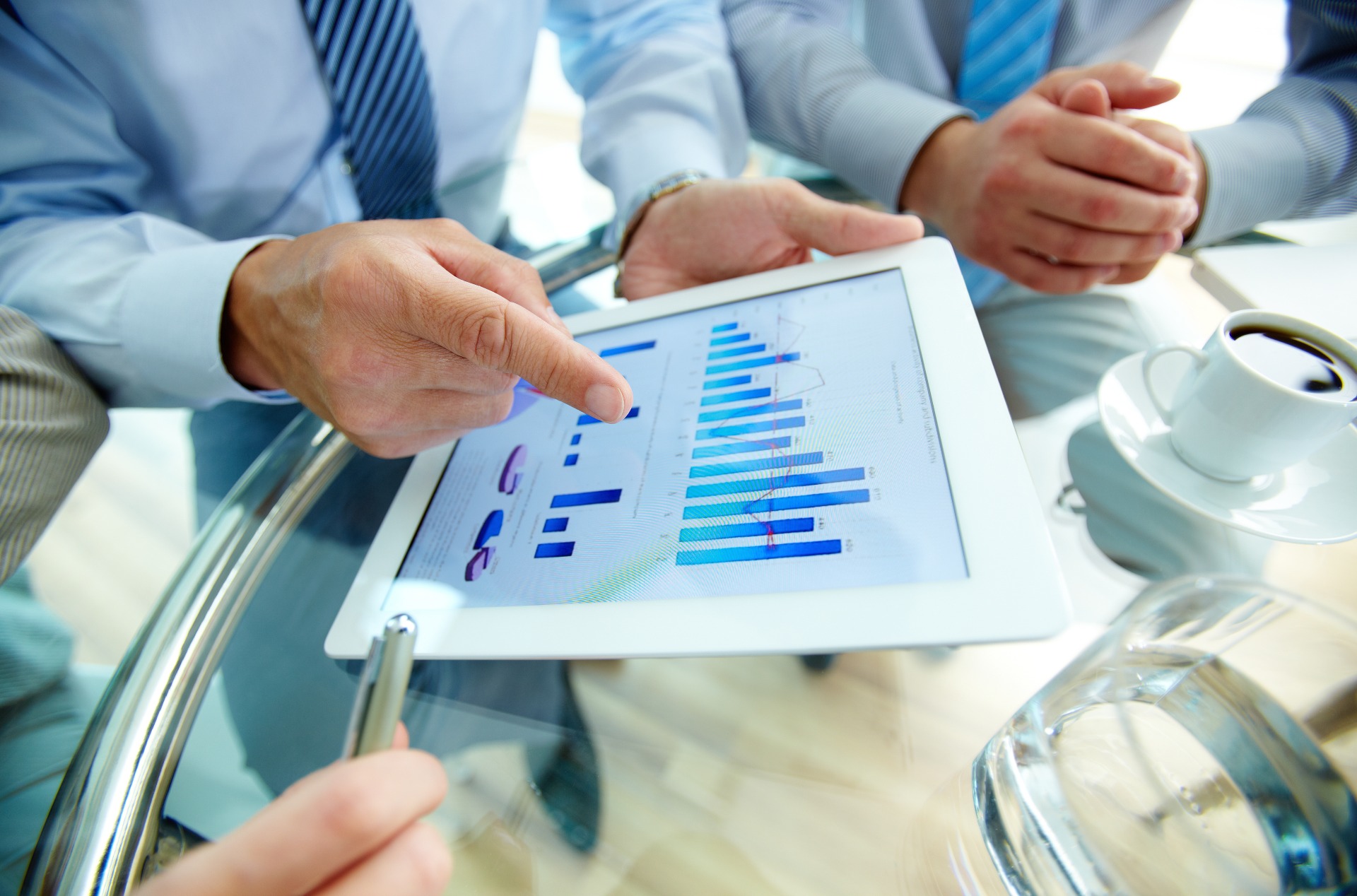
Tudástár
„A kreatív gondolkodás innovatív produktummá válik!”
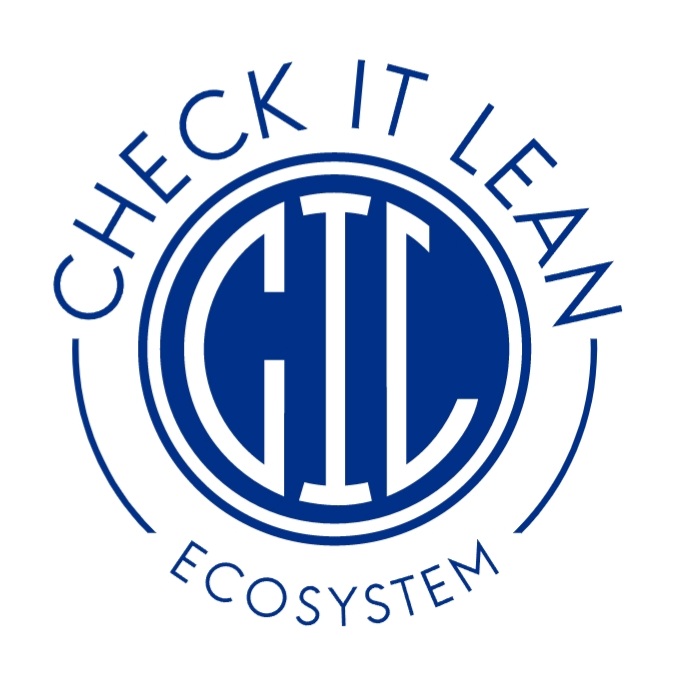
Tudástár
5S
Az 5S módszertan lényege, hogy segítségével megteremtjük a Kaizen tevékenység (folyamatos jobbítás) alapját, amely által javítjuk folyamataink áttekinthetőségét és fejlesztjük a munkabiztonságot, a minőséget. Az 5S módszertant alkalmazhatjuk a gyár bármely területén. Az 5S nem egy egyszeri akció, hanem egy tartós folyamat, melyet rendszeresen felül kell vizsgálnunk (Audit), ezáltal a folyamatokban lévő látható vagy rejtett problémák feltárását segítjük elő.
Elemei:
- Szortírozás (szüntesse meg azt, amelyre nincs szükség).
- Rendezés (a megmaradt elemek rendezése).
- Tisztítás, takarítás (tisztítsa meg és ellenőrizze a munkaterületet).
- Szabványosítás (hozzon létre szabványokat).
- Fenntartás (a szabványok rendszeres alkalmazása)
7 + 1 veszteség
Minden olyan tevékenység, amely nem nem hozzáadott érték a folyamatban, veszteségnek minősül, amiért a Vevő nem fizet. A Lean segítségével a folyamatokban lévő 7 + 1 veszteséget akarjuk eltávolítani.
1. Várakozás
2. Szállítás
3. Utómunka
4. Túlkészletezés
5. Túlgyártás
6. Felesleges mozgás
7. Felesleges tevékenység
8. Ki nem használt emberi erőforrás
A3
Szabványosított eszköz a PDCA logika használatához. A probléma kiváltó okainak elemzéséhez, valamint a probléma megoldásához szükséges intézkedések helyes meghatározásához és végrehajtásához kell vezetnie.
Andon
Vizuális visszacsatoló rendszer, amely jelzi a gyártás állapotát, figyelmeztet, amikor segítségre van szükség, és felhatalmazza az üzemeltetőt a gyártási folyamat leállítására.
Szűk keresztmetszet
A gyártási folyamat azon részét nevezzük "szűk keresztmetszetnek", amely korlátozza az általános teljesítményt, a gyártás hatékonyságát.
Folytonos áramlás
Gyártás, ahol a folyamatban lévő munka zökkenőmentesen folyik, minimális és meghatározott (vagy akár nulla) pufferekkel a gyártási folyamat lépései között.
Gemba (az igazi hely)
Azon hely, ahol valódi cselekedetek történnek, az értékteremtés helye.
Heijunka (szintezés)
A termelési ütemezés, kiegyenlített termelés. A gyártott típusok és mennyiségek kiegyenlítése. Alkalmazásával a készletek, ennélfogva az átfutási idők is jelentősen lecsökkennek. Gyártási rendszerünk rugalmasabb lesz, így könnyebben tudunk reagálni a vevői igények változására.
Jidoka (önállóság)
Automatizálás a gyártásban. Egy olyan rendszer leképezése, amely észleli a gyártási hibát és azonnal megállítja a gépet, technológiát, folyamatot. Így elkerüljük a selejt termék előállítását.
Időben történő szállítás - Just In Time (JIT)
Cél csökkenteni az átfutási időt és a készletet. Jelentése: Minden termék amely a gyártáshoz szükséges, álljon rendelkezésre a megfelelő időben, a megfelelő mennyiségben és a megfelelő helyen.
Just In Sequence (JIS)
A Just-in-time kifinomultabb formája. A Vevő összeszerelési sorrendjének leképezése a gyártásba. A folyamatoknak stabilnak kell lenniük a szállítási problémák elkerülése érdekében, mivel szinte nincs gyártásközi készlet.
Kaizen (folyamatos fejlesztés)
Olyan stratégia, amelyben az alkalmazottak proaktív módon működnek együtt a gyártási folyamat rendszeres, fokozatos javításának elérése érdekében. Jelentés: változtasson ("kai") jobb ("zen") helyzetre. A kreatív gondolkodás innovatív produktummá válik.
Kanban (Pull System)
Az áruk áramlásának szabályozására szolgáló módszer mind a gyáron belül, mind a külső szállítók és ügyfelek között. Az automatikus feltöltés alapján olyan jeleken keresztül, amelyek jelzik, hogy mikor van szükség további árukra. Eszközei: Kártya, tábla, dokumentum ("Kanban").
KPI (Key Performance Indicator)
A szervezet kritikus célkitűzései felé történő haladás nyomon követésére szolgáló teljesítmény mutatók összessége.
Line Balancing
A művelet terhelésének a Takt-időhöz való maximális kiegyensúlyozása a szűk keresztmetszetű munkaállomások elkerülése érdekében. Ennek a megközelítésnek a maximális hatékonysághoz és a legalacsonyabb beruházási költségekhez kell vezetnie.
Muri, Mura, Muda (3Ms)
Bármi a folyamatban, amely a Vevő szempontjából nem nyújt hozzáadott értéket. Az általános irodalom három típusú veszteséget különböztet meg: Muri (túlterhelés), Mura (egyensúlyhiány), és Muda (hulladék, 7+1 típusú hulladék).
Teljes berendezés hatékonyság (OEE)
Az adott gyártási folyamat termelékenységi veszteségeinek mérésére szolgáló keretrendszer. A veszteségek három kategóriáját követjük: rendelkezésre állás (pl. gép, folyamat leállási idő), teljesítmény (pl. lassú ciklusok), minőség (pl. selejt, utómunka, Vevői elutasítás). Az OEE meghatározása testreszabott és adaptált minden vállalat számára.
PDCA (Plan, Do, Check, Act)
Iterációs módszer a fejlesztések végrehajtására.
A PDCA-ciklus lebontása:
• Plan - Terv: Adjon meg egy problémát és dolgozzon ki lehetséges megoldásokat.
• Do - Csinál: Hajtson végre egy javasolt megoldást, jobbítást.
• Check - Ellenőrzés: Értékelje az eredményeket, hogy megtudja, működik-e egy megoldás, jobbítás.
• Act - Teendő: Hajtsa végre a két művelet egyikét: térjen vissza a tervezési lépéshez, ha az eredmények nem kielégítőek, vagy szabványosítsa a megoldást, ha az eredmények elegendőek.
Poka-Yoke (Hibaelhárítás)
Tervezze meg a hiba észlelését és megelőzését a termelési folyamatokban azzal a céllal, hogy nulla hibát érjen el. "Bolond biztos" módszer kidolgozása, amely segíti a munkavállalót a pontos, veszteségmentes munka elvégzésében.
Kiváltó okok elemzése, Gyökér ok elemzés
Problémamegoldó módszer, amely a mögöttes probléma megoldására összpontosít, ahelyett, hogy gyors javításokat alkalmazna, amelyek csak a probléma azonnali tüneteit kezelik. Általános megközelítés az ötszörös kérdés megkérdezése, 5 miért - mindegyik lépéssel közelebb kerülve a kiváltó ok felfedezéséhez. Így elkerülhető, hogy a hiba megismétlődhessen.
Egy perces szerszámváltás (SMED)
Lépései:
Cél: Átállási idő <= Műveleti idő.
1. szint: Műveletek elemzése, videó felvétel készítése.
2. szint: A Külső és a Belső műveleti idők szétválasztása.
3. szint: A Külső idők műveleteinek strukturált átszervezése.
4. szint: A Belső idők Külső időkbe történő átrakása.
5. szint: Belső idők folyamatos csökkentése - Folyamatos fejlesztés.
Külső Idők: Olyan lépések, amelyeket el lehet végezni a gép működése közben.
Belső Idők - Olyan lépések, amelyeket csak a gép leállása mellett lehet elvégezni.
Az olyan folyamatokban, mint például a sorozatgyártás, a Takt-on belüli átváltás a nagy rugalmasság célja.
Hat nagy veszteség
A termelékenység csökkenésének hat kategóriája, amelyet szinte egyetemesen tapasztalunk a gyártásban:
1. Szünetek
2. Beállítás / Korrekciók
3. Rövid megállások
4. Csökkentett sebesség
5. Beállítási selejt
6. Gyártási selejt és utómunka
Szabványosított munka
Dokumentált gyártási eljárások, amelyek rögzítik a bevált gyakorlatokat. Könnyen megváltoztatható "élő" dokumentációnak kell lennie.
Takt idő
A gyártás üteme (például egy darab elkészítése 34 másodpercenként), amely összehangolja a gyártást a Vevői igényekkel. Tervezett gyártási idő a Vevői igény szerint számolva.
Tervszerű teljeskörű karbantartás (TPM)
Átfogó megközelítés, amely a proaktív és megelőző karbantartásra összpontosít az OEE maximalizálása érdekében. A TPM-el a karbantartás és a gyártás határai létrehozhatóak.
Toyota gyártási rendszer (TPS)
Gyártási stratégia, melyet a japán Toyota Motor Corporation fejlesztett ki sok éven át. A TPS az átfutási idő csökkentésére összpontosít a folyamatokban lévő veszteségek eltávolításával és csökkentésével. Elősegíti a LEAN alapú gyártást, termék előállítást.
Értékfolyam-leképezés (VSM) / Értékfolyam-tervezés (VSD)
Ezt az eszközt a folyamat, az anyag és az információ áramlásának vizuális leképezésére használják. Megmutatja a folyamatok jelenlegi (VSM) és jövőbeli állapotát (VSD) oly módon, hogy kiemelje a fejlesztési lehetőségeket.
Visual Management
A gyártóüzemben használt vizuális kijelzők, kezelőszervek, információs táblák, jelölési rendszerek (pl. színjelölés, feliratozás) az információközlés javítása érdekében. Példák: padlójelölés, lámpák, táblák, KPI táblák, min / max táblák, andon jelek stb.)
Innováció
Egy Vállalkozás eredményessége a legnagyobb részt az időzítésen múlik, ezt követi a csapat minősége, majd pedig a kiváló alapötletek megléte.
2017-től a Vállalkozások egyre nagyobb igénnyel álltak elő a Folyamatos Fejlesztés iránt. A Vállalkozások szembesültek a Vevői igények folyamatos növekedésével a fejlesztési és gyártási költségek csökkentése mellett. Mára kialakulóban van egy új innovatív gyártási rendszer, amelynek alapja a LEAN alapú gyártás. Ez a növekedés, fejlődés nem tartható fenn elhivatottság, szakértelem, pontosság és kreativitás nélkül. Megfelelően dokumentált intézkedések, a gyártási- és technológiai problémákra való gyors reagálás, a napi következetes ellenőrzések, után követések meghozzák a várt eredményt és Vállalkozása a "Jövőbe lép"!
Six Sigma
A SIX SIGMA nem a LEAN, hanem a Folyamatos Fejlesztés egy eszköze a hatékonyság növelésére, a költségek csökkentésére. A Six Sigma egy vállalatfilozófia, amely fókuszában a strukturált problémamegoldás és minőség fejlesztő tevékenység áll, amely során a folyamatban lévő hibák és veszteségek számát és arányát nullára csökkentik.
A Six Sigma módszer 5 lépésből áll, amelyek a Definiálás (Define), a Mérés (Measure), az Analízis (Analyze), a Fejlesztés (Improve) és a Kontroll (Control) = DMAIC.
A fejlesztés során mérik a Sigma-t, azaz a folyamat ingadozását, szórását. Egy folyamat annál jobb, minél kisebb az ingadozás, a szórás, azaz minél nagyobb a Sigma.
A folyamatos tökéletesítésre való törekvés létrehozta azokat a mutatókat, amelyek egyértelműen leírják a folyamatok minőségének eredményét. Ezen mutatók a PPM (Parts Per Million) és a DPMO (Defect Per Million Opportunities).
A PPM jelentése: Egymillió legyártott termékben keletkező hibás termékek száma.
A DPMO jelentése: Az egymillió hibalehetőségre eső hibák száma.
Ezzel minden olyan folyamat mérésére lehetőségünk nyílik, ahol hibát lehet elkövetni.
A SIX SIGMA-ra úgy kell tekinteni, mint egy olyan mérföldkőre a fejlesztési folyamatban, amely a fejlődés irányát és útját hivatott megmutatni.
CHECK IT LEAN - Your Professional Partner